Turning plastic waste into roofs in Burkina Faso
Published 8 November 2016 by Caroline Grellier
Plastic wrappings are a plague in Africa. Not for the Cameroonian engineer Calvin Tiam who developed a roof coating made from plastic waste. He is developing his prototype in Burkina Faso. Meeting.
Ouagadougou, from our correspondent (text and photos)
A true environmental plague in Africa, plastic wrappings are everywhere. It seems impossible to stop their consumption overnight or the habits of populations that go with them. Calvin Tiam, Cameroonian engineer in industrial process technology and renewable energy, on the contrary, sees an opportunity to produce sustainable materials with local raw material and cheaply.
Material, ok, but to do what? You just need to walk round the neighborhood where Calvin Tiam started his young company to come across another African issue: roofing materials. A large majority of homes in Ouagadougou are covered in corrugated iron. A makeshift roof, ill-adapted to the Sub-Saharan climate, that produces more heat. As a result: inside the homes, the temperature easily reaches 50°C and this heating discomfort is detrimental to inhabitants’ quality of life.
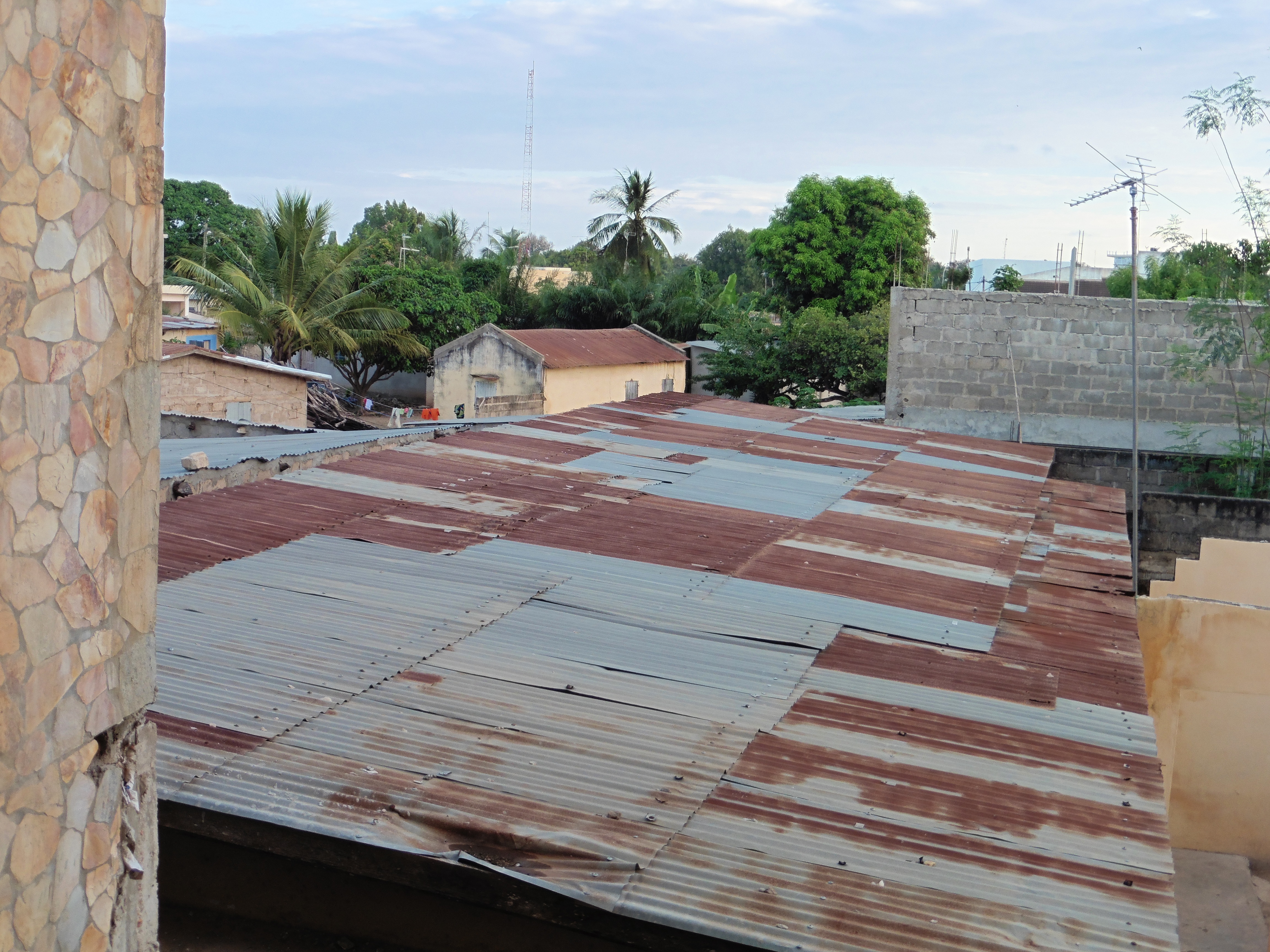
In 2011, Calvin Tiam develops a roof coating made from used plastic. In order to further his project and complete his business plan, the young entrepreneur joined the 2IE incubator in Ouagadougou to create his company TECO2 (‘Toiture ECOlogique et ECOnomique’- ECOlogical and ECOnomical roofing). “Made locally, this material considerably recycles polyethylene plastic waste, explains the young engineer. One square meter of TECO2 coating represents around 10kg of recycled plastic, thus a decrease of 9kg of CO2 equivalent of greenhouse gas in nature.”
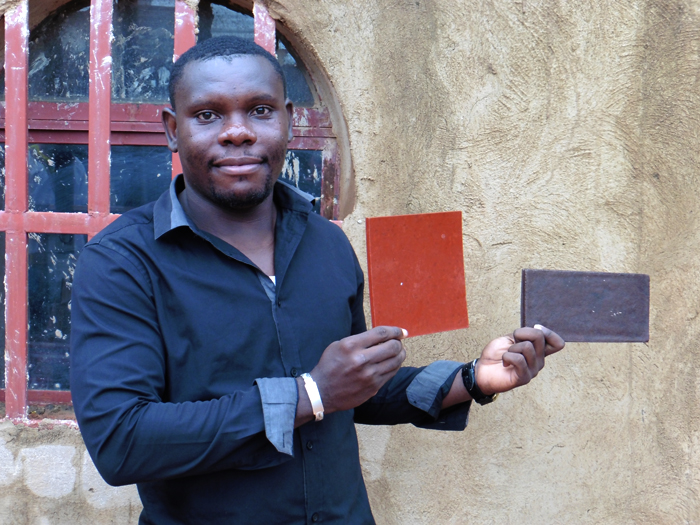
Up to 400 time more insulating than corrugated iron, his plastic panel offers better heating comfort and allows you to considerably decrease electricity consumption by reducing the use of ventilation systems or air-conditioning units. Esthetically, the finish is amazing: colored material, a smooth touch due to the extrusion process or much rougher with thermo-compression. In both cases, we forget its plastic origin, which seduces the local population.
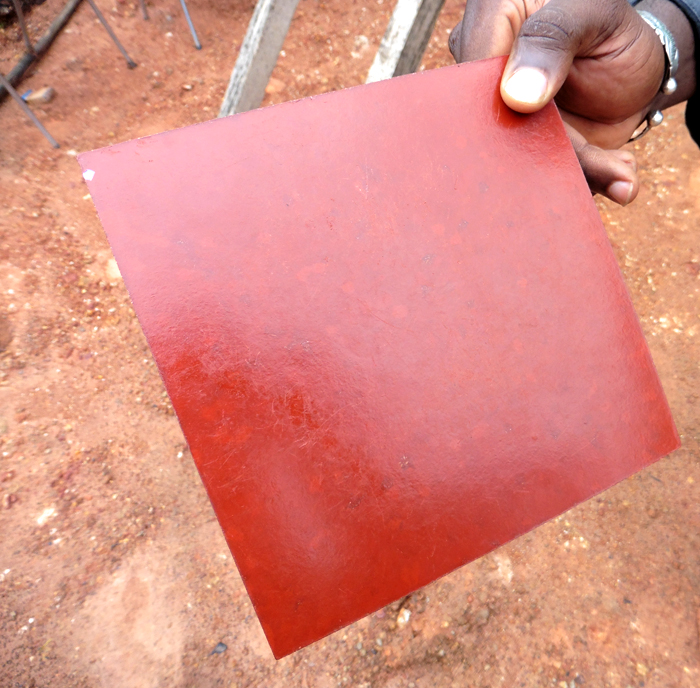
Calvin Tiam is currently finishing his prototypes with help from several laboratories (LEMC of the 2IE in Burkina Faso; Pimm from the Paris Tech Arts and Crafts and GFMP from Itech Lyon in France) and making sure that his transformation process does not release any noxious gas in the environment. He did not hesitate to call on the Ouagalab, Burkina Faso’s fablab, to print his panel prototypes for example in order to study its shapes.
His semi-traditional production unit is being built and has already acquired some equipment. The young entrepreneur ambitions to recycle 500 tons of plastic within one year to deliver a suitable roof for some 1,300 households. Calvin Tiam’s concern is to contribute to the socio-economic development of the country by eventually creating twenty or so jobs within his company. “In order to do this, I am presently seeking financial backup and partners to begin series production and carry out a comprehensive review of the performances of the material through the building of a pilot home.” If you catch my drift…
Fore more information, contact Calvin Tiam