What can we learn from the makers who organized to locally produce open source respirators?
Published 27 September 2021 by Bérengère Fally
Early in the Covid-19 pandemic, makers across France and Belgium got organized to tackle the shortage of medical equipment by prototyping open source ventilators. How did these makers coordinate their tasks? With whom did they collaborate? What technologies did they use? How was information exchanged? Where do the projects stand today? Is this “innovation”?
Correspondence, Bérengère Fally and Robert Viseur, UMONS
This survey is based on the results of an ongoing research project, conducted within the framework of the FabricAr3v Interreg project covering the geographical area of France, Wallonia and Flanders. It aims to understand the territory’s potential to adopt small-scale manufacturing technologies, how collaborations around open source and open hardware are organized, and the potential to further develop local low-cost production and stimulate activity.
The initial pandemic situation on the ground
In March 2020, despite gradually increasing lockdowns, Covid-19 was spreading exponentially in Europe, where healthcare systems were rapidly reaching their limits. The unexpected growth of the pandemic highlighted the lack of organization and resources to treat patients who were overwhelming hospitals.
At the height of the health crisis, this lack of resources was particularly evident in the case of masks (such as FFP2s), accessories (such as syringe pumps), and ventilators, which was problematic for health workers worldwide. It was almost impossible to acquire equipment that conformed with European standards. Stocks were low, and local production capacity struggled to meet demand, which underlined European countries’ dependence on foreign countries such as China.
A new kind of local dynamic developed around the world to make up for this shortage. Local makers quickly mobilized human resources to contribute a wide range of expertise across various sectors, with a single objective: to help healthcare workers fight the pandemic under better conditions. Meanwhile, small-scale manufacturing devices, such as 3D printers and open source microcontrollers, rapidly solved the shortage of medical supplies at the local level.
By giving free access to data commons (source codes, maps, etc.) shared through online platforms, makers disseminated information and tutorials, so that anyone with access to digital manufacturing tools such as 3D printing could easily reproduce out-of-stock basic sanitary protective gear (such as face shields) at low cost.
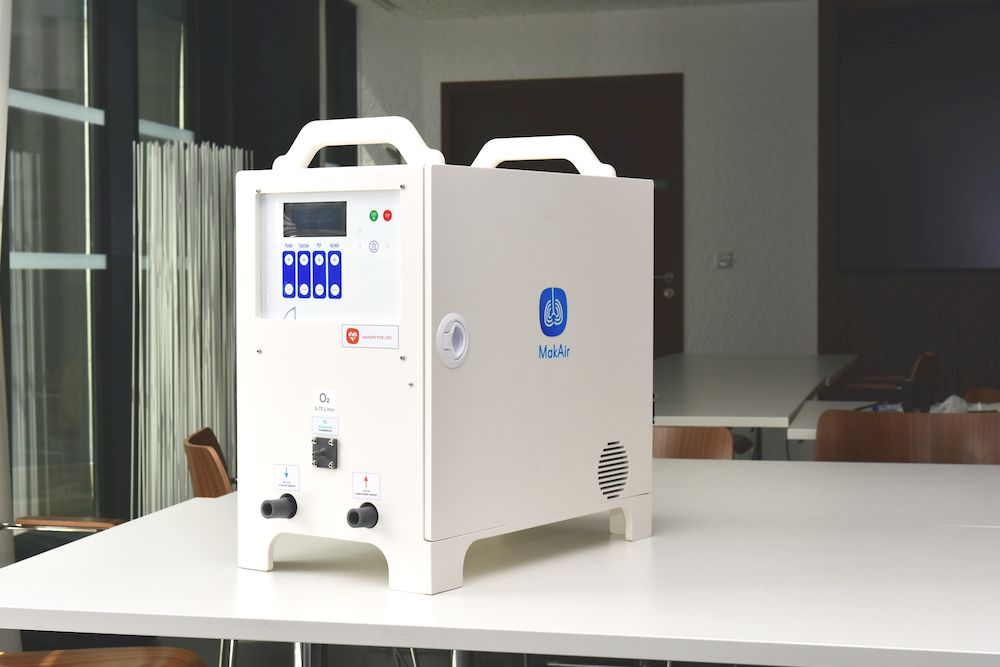
Making ventilators, those complex medical devices
Makers also collaborated to develop more complex devices, such as ventilators and their accessories. Ventilator equipment was generally available, but supplies dwindled as the number of patients increased, and the virus caused critical damage to patients’ lungs. As the number of Covid-19 cases and hospitalizations skyrocketed, this shortage of medical equipment threatened to jeopardize the proper workflow of hospitals, especially when the supply chain was no longer following.
Moving on from producing conventional medical supplies such as face shields to develop open source ventilators was a challenge for makers. Ventilators are complex medical grade devices that require a variety of tests and certifications before they can be used on a patient in respiratory distress. The patient’s vital functions depend directly on the device’s reliable operation.
Respiratory assistance devices are mainly produced by industrial manufacturers, and incorporate components that allow for very precise adjustments to all controllable parameters. There exist basic, easily transportable, non-invasive devices, as well as very advanced invasive mechanical ventilation devices that have taken years to develop, with many modes of ventilation and control, a large display showing respiratory flow, pressure, volume, etc. Prices vary between 10,000 euros for small models and 40,000 euros, or even much more, for sophisticated models.
Early in the pandemic, and even today in countries where the spread of the virus is once again intensifying, numerous statistics explain how the need for ventilators can quickly exceed availability if nothing is done to boost production and distribute supply.
One of the leading manufacturers of respiratory aids in Europe is Hamilton Medical. During the March 2020 lockdown in Europe, this Swiss company increased its production by 50% to meet hospitals’ demand of 1,200 to 1,500 units within a few weeks (the same number of devices usually produced within a year). The company was unable to meet the demand, not only because of limited production capacity, but because it was unable to obtain essential components, as many countries had banned the export of certain medical equipment to prevent domestic shortages.
This situation revealed how these recurrent and now predictable shortages are due to a dependence on globalized supply chains for medical products and their inequitable distribution. The crisis demonstrated the limits of such a global value chain and created an opportunity for strategic options that could lead to more resilient and diverse supply chains, both locally and regionally.
The shortage of ventilators in March 2020, coupled with manufacturers’ inability to quickly produce machines and/or put them on the market at affordable prices, led many makers to collaborate on developing a device that automates the manual ventilation process for patients in critical situations where there are not enough ventilators available.
Given the complexity of this type of specialized medical equipment, these makers coordinated with various actors (researchers, entrepreneurs, nursing staff, etc.) in order to make up for the shortage in different ways, even if there was no perfect solution.
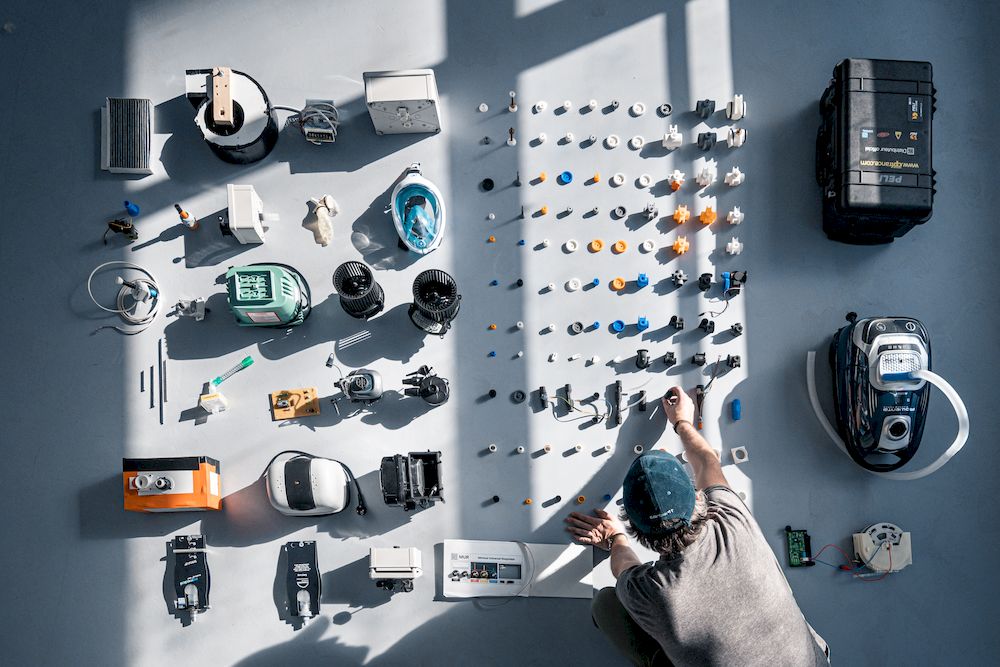
Many open source ventilator projects were developed by makers during the Covid-19 pandemic with the sole objective of countering the shortage and saving lives. An analysis of open source respirator projects, Free-Libre Open Source COVID-19 Pandemic Ventilator Projects, identified 143 projects around the world at the peak of the pandemic. The majority of these projects have remained in prototype stage, while others have been approved and used in real-life situations.
Makery covered the topic of ventilator prototyping between March and December 2020 in several articles: OxyGEN, UCL-Ventura, M.U.R. and MakAir.
Makery’s coverage also includes the scientific research carried out within the framework of the Interreg FabricAr3v project and extends to other open source ventilator projects prototyped in France-Wallonia-Flanders: “Riot respirator”, Breath4Life and EPICura. The most informative projects were further contextualized with interviews and existing scientific literature.
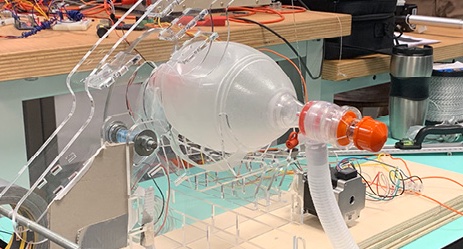
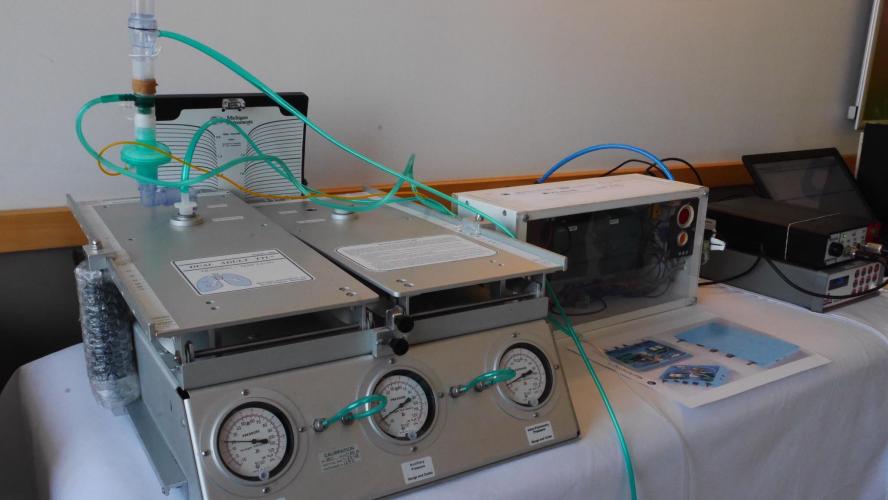
How the makers got organized
This collaboration of makers on open source ventilator projects was organized into an ecosystem, precisely to resolve the complexity of open hardware prototyping through 3D printing, digital technology and open innovation. The design process and knowledge flow was enriched by contributors from all disciplines with diverse skills. Gathered in communities and motivated by collective innovation, these various profiles valued the use of open source and open hardware tools to develop practices and innovate locally for a larger-scale impact. Free access to data commons (source codes, maps, etc.) via online platforms facilitated exchanges and organization among the various circles.
One example is how the local maker community got organized to develop the open source Breath4Life respirator in Belgium. This project was initiated by makers, UCLouvain researchers and doctors who wanted to help combat the medical crisis using new technologies applied to the medical field. The prototype was built at MakiLab, the university fablab at UCLouvain that coordinated the project. The roles were distributed naturally in a dynamic collaboration between academic research (UCLouvain), maker communities (OpenHub, MakiLab), industrial suppliers (Coexpair, Covartim, Elia, IBA, Odoo, ATLR Engineering, etc.) and operators from the medical field (Jolimont Group and Saint-Luc University clinics), in order to locally produce open source medical equipment.
For such projects, spaces such as fablabs and makerspaces played a mediating role between makers and their institutional partners. Additionally, global platforms for international maker projects, for example at MIT, provided reference designs.
Collaborative projects for open source ventilators
On all these projects, 3D printing was predominant, and the open source maker mentality allowed for distributed contributions, where each person could get involved at their own level.
While many saw maker initiatives as a temporary solution while waiting for the industry to reorganize, it’s clear that communities of tech innovators provided practical solutions to medical equipment shortages, and demonstrated the value of digital manufacturing technology to people who need it in the field.
According to the analysis, one of the main challenges encountered by the developers of the open source ventilators was organizing the often remote contributions of each person involved, given the pandemic conditions. Using Telegram, Slack, GitHub, Riot (Element) and other online messaging tools, makers distributed the work among several different actors who were geographically located in different places.
The majority of developers of open source ventilators were able to save precious time by openly sharing knowledge and information exchanged online. Thus, they could already control how the devices would be used, in cases where security was a key aspect of their deployment. It should be noted that in practice, some projects simply do not publish the plans or only disclose parts of them (in order to formally announce the project, to avoid excessive optimism, to distance the project from maker culture, to better control its uses, etc.). The complexities involved in producing ventilators revealed real problems in terms of structuring and knowledge sharing, especially when it came to codifying practices.
But for all the ventilator prototypes developed, digital technology played a fundamental role. Whether in terms of communication and exchanges or in terms of production, digital tools were at the core of collective action and the creation of common knowledge. The health crisis pushed makers to largely adopt open intellectual property, as part of the pursued objective of social innovation, while the combined situation of lockdown and crisis fostered the use of effective communication tools for abundant documentation (texts, videos, plans, drawings, tests, etc.). The unifying force of a common goal during extreme conditions has created a rich digital commons that is now available to all.
Success of the open source MakAir
The most successful and efficient ventilator project in terms of innovation, organization and learning is the MakAir.
It was developed by the “Makers for Life” consortium, which mobilized a strong network of field experts, including manufacturers, and was supported by the French Atomic Energy and Alternative Energies Commission (CEA) as well as the Defense Innovation Agency (AID). This project quickly took on interesting industrial and international dimensions, serving as an inspiration to federate an open source community.
From this virtuous ecosystem emerged the importance of engineering and clear specifications, followed up by rigorous project management. Even just recently, 100 MakAir units were produced by SEB and shipped to India, further underscoring the value of innovation in engineering.
MakAir’s industrial production goal in no way undermines its open source character. The advantage of such a project is that all its components can be remotely reconfigured to meet specific needs, and each unique case improves MakAir’s overall development.
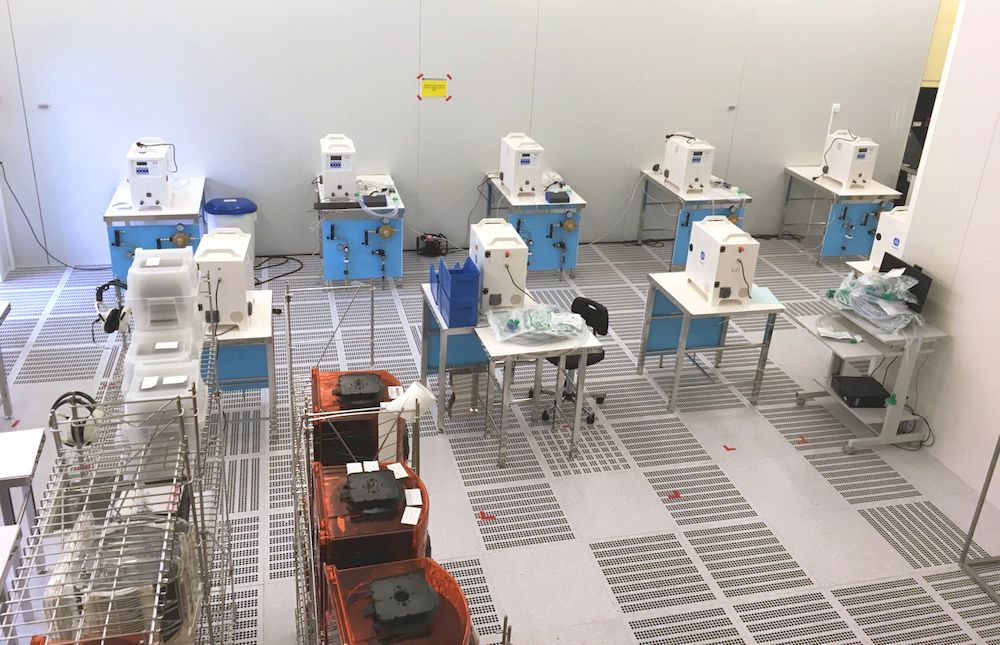
Ingenious solutions in hostile conditions to do more with less
With the goal of facilitating local manufacturing at low cost, the principle of innovation is to improvise ingenious solutions under adverse conditions.
From an operational point of view, this can also be seen in the development of simpler ventilator projects that can be more easily repaired and have reusable parts. This simple, sustainable and quality mode of innovation requires specific engineering that targets the minimal use of natural resources and doing more with less. This results in a relatively simple technological build that still meets a specific need. It requires clearly identifying needs in the field, focusing on essential functions, being familiar with existing applications and minimizing manufacturing and distribution costs. This certainly reflects the needs of developing countries, as well as the growing need for more localized production.
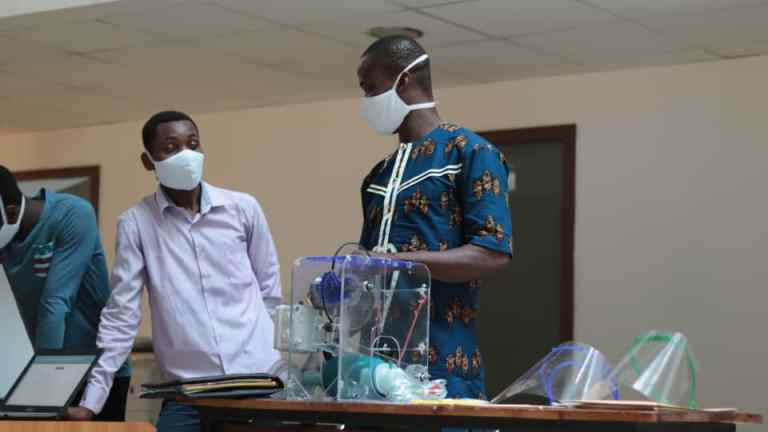
Prospects for open hardware rapid prototyping
The way the community organized itself to prototype these open source ventilator projects is a prime example of the transdisciplinary dynamics that can rally makers, volunteers (researchers, students, citizens, medical staff, etc.), academics, actors in the health sector, global scientific research, corporate players, etc., as well as the type of governance capable of ensuring that knowledge is shared in compliance with professional contracts and open source standards.
The ability of makers to organize collectively in order to acquire technological knowledge and apply it effectively to combat the pandemic emphasizes innovative low-cost prospects in Open Medical Hardware, as well as a new type of local organization for small-scale production, featuring additive manufacturing, upstream a more industrial type of production.
However, although the formalities required for approval are understandable given the vital operation of the ventilator for a patient’s survival, the makers behind these projects encountered many difficulties when attempting to validate their prototype. These included obtaining precise and understandable information on the procedures to be followed, access to test benches, validation deadlines, etc., which prevented most projects from succeeding. Without denying the need for a legitimate framework for development, regulations need to be more accessible, clearer and less rigid. The procedures were designed for drugs and well-establshed devices and are not suited to digital technological innovation, which favors iteration and agility.
By digging deeper into the topic of open source ventilator prototyping, we can better assess how well certain projects favor appropriation of technologies, organization and learning to demonstrate resilience and face the pandemic with new strategies for innovation and development. These new ways of working can in turn lead to products with renewed value, newly created entrepreneurial activity, industrialization, or methodologies that can be deployed in developing countries.
FabricAr3v
This research work on open source ventilators was developed during the Covid-19 pandemic, funded by the European Interreg program as part of the FabricAr3v project. The latter is dedicated to the development and promotion of low-cost and open hardware 3D metal printing technology. The research carried out here has made it possible to analyze and better understand how open hardware innovation projects are organized.
Learn more about the Interreg FabricAr3v program supported by the European Regional Development Fund
Read Makery’s articles on the maker mobilization against Covid-19