Fabtextiles weaves biology into textiles in Barcelona
Published 28 June 2019 by Catherine Lenoble
Interweaving digital fabrication, textile design and open science, Fabtextiles in Barcelona is a pioneering fablab for biomaterials.
Barcelona, chronicle
The (fast-)fashion industry has long been the world’s second most polluting industry (after oil). Fabtextiles, launched in 2013 as a special project by Fablab Barcelona, researches and finds solutions to transform creation, production and distribution: “instead of waiting for things to change, modifying them at the root”.
Sharing space with the Institute for Advanced Architecture of Catalonia (IAAC) in the Poblenou Maker District, Fabtextiles resonates with the fabcity dynamic, connecting activities by the local maker community with the worldwide network of fablabs specializing in fabric and materials design.
Learning Expedition
Fabtextiles opened its doors to us for a Learning Expedition, a multidisciplinary research pole around “future technological disruptions in the fashion and textile sector” organized in Biarritz by Chaire Bali. Chaire member participants included teachers and former students of ESTIA engineering school, the director of the European Center for Innovative Textiles and a representative of the brand Nabaji (Decathlon).

I participated in the adventure on behalf of Funlab (citizen fablab in Tours) with Hors-Studio, a textile/surfaces/materials design studio founded by Funlab members Rebecca Fezard and Elodie Michaud. The two-day program began with a presentation of Fabtextiles followed by a prospective workshop and a visit to the International Textile Machines Expo (Internationale Textilmaschinen Ausstellung, ITMA).

Fabtextiles biorecipes
After graduating from IAAC in 2011, Anastasia Pistofidou initiated Fabtextiles two years later. With the firm conviction that frantic production and mass consumption needed to be reoriented toward local manufacturing that is better adapted to our everyday lives, Anastasia and now a whole community happily mix genres and techniques: circular economy and fashiontech, handcrafts and sensors, dyes and bacteria.

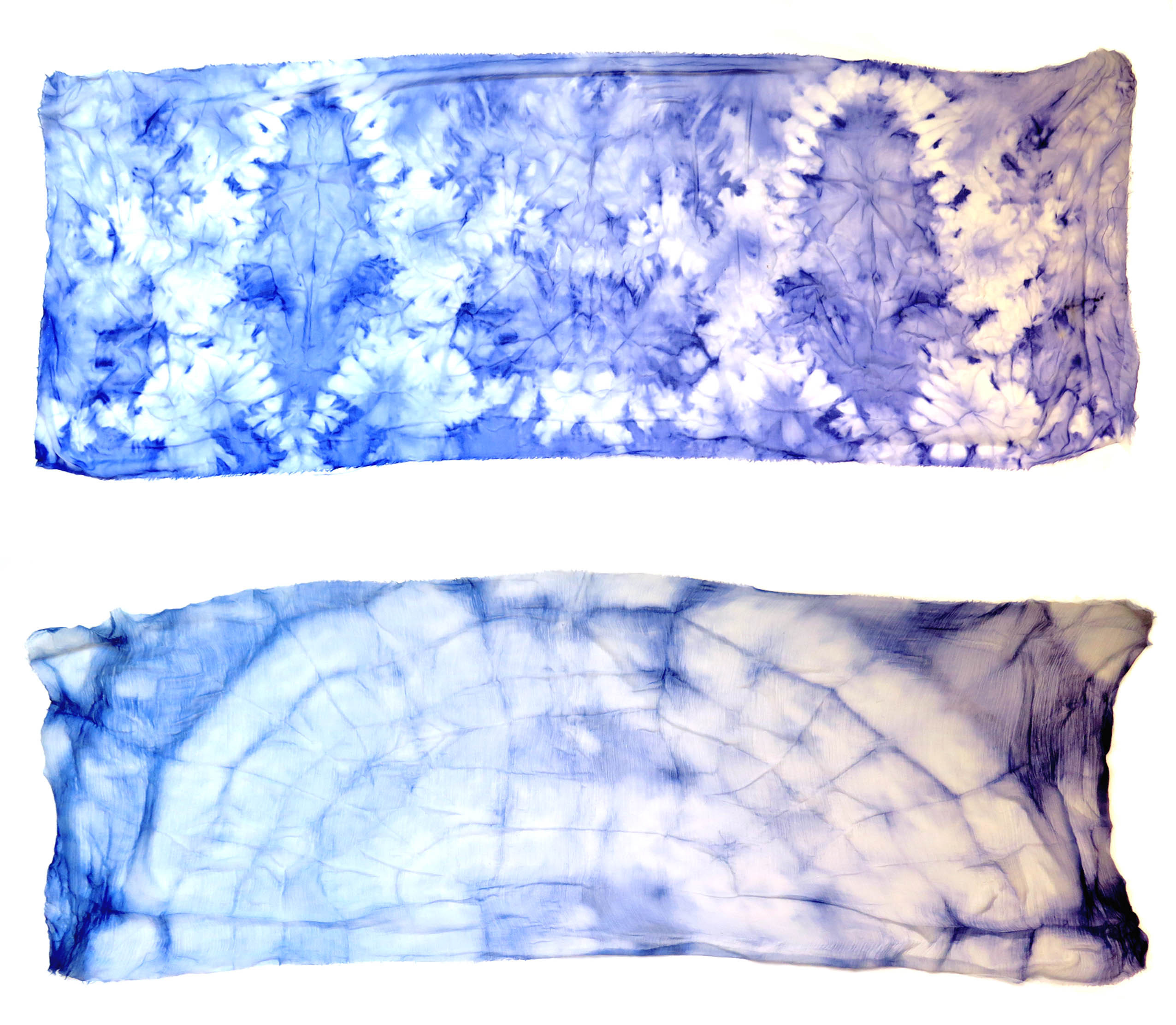
During Anastasia’s presentation, we were able to touch and feel various prototypes developed in the lab: dyes, a collection of biobags made from laser-cut biodegradable materials, samples of 3D-printed fine mesh, a library of bioplastics, shoes with 3D-printed soles, bags made of wood and fabrics designed to be customized in local fablabs.

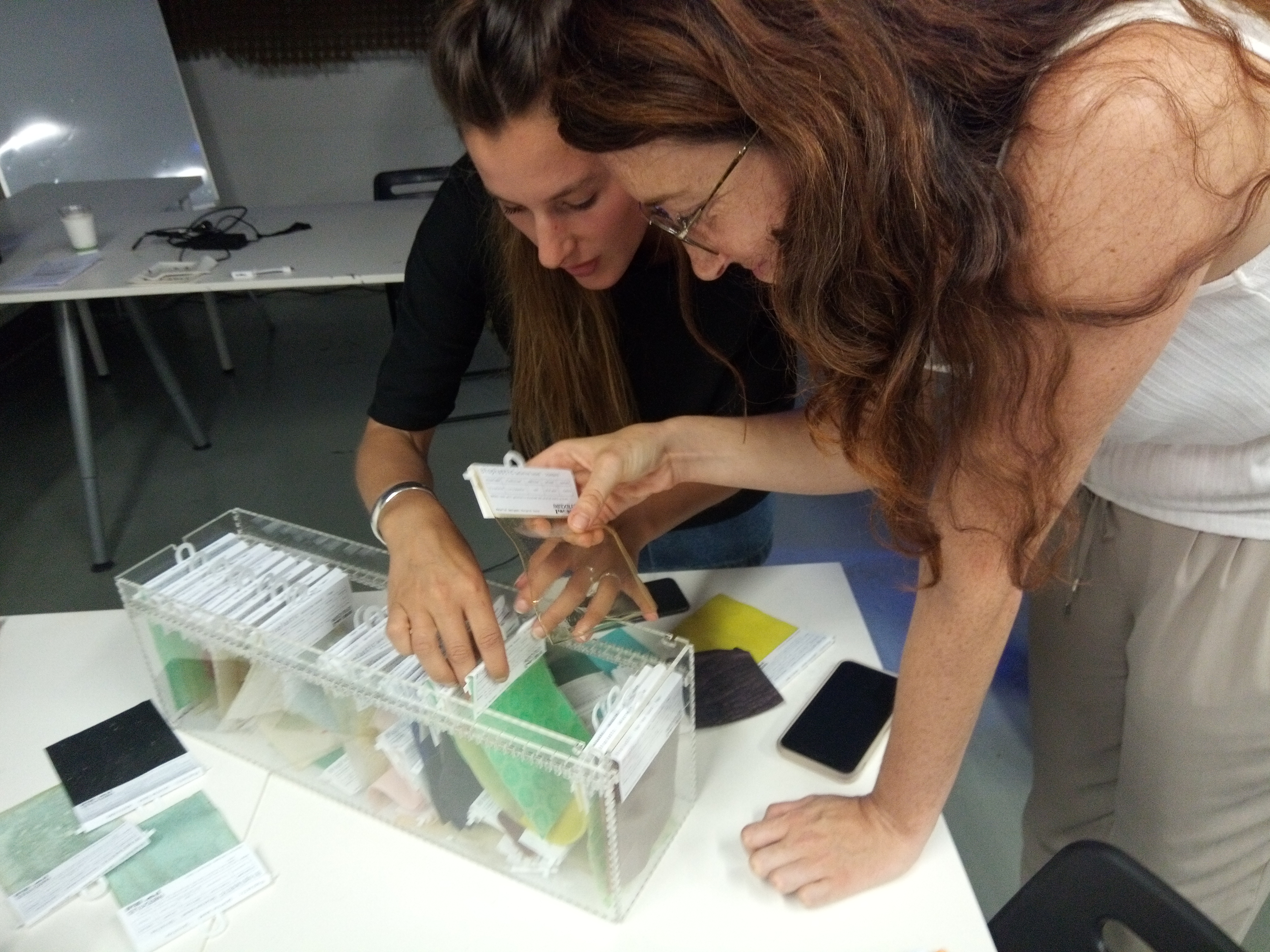
Future jobs in biomaterials
While Fabtextiles continues to experiment, Anastasia furthers the movement through education. In 2017, she launched Fabricademy, an annual distributed and international six-month course that merges open source, digital fabrication and biomaterials. Fabricademy is deployed in 18 other “node” fablabs, including in France, Fablab Digiscope in Paris-Saclay and soon Sew&Laine, a space for “activist textile cultures” in a former DDP factory outside Bordeaux.
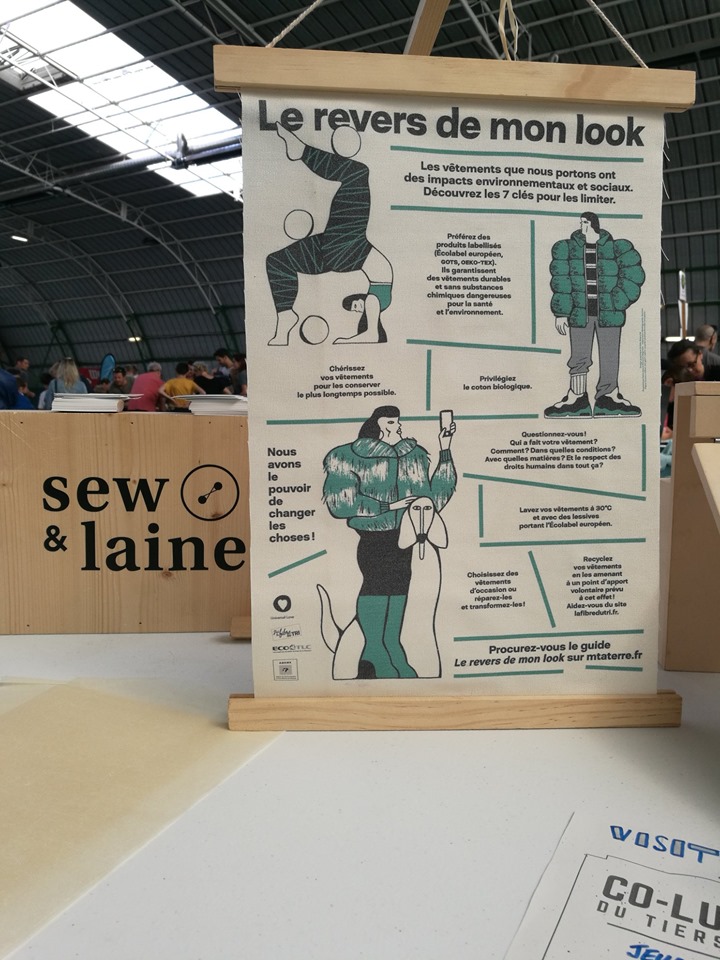
Our own prospective workshop, led by a teacher and researcher at ESTIA, was about future professions in the fashion and textile industry. We imagined data visualizers, bio makers and circular designers, all part of a distributed model to make your own tailored garment in the local fablab with biosourced materials.
Biocuisine
After the workshop we visited Fablab Barcelona, which offered machine-tools and workshop extensions just across the street. I asked Anastasia’s colleague Marion Real about one of the bags that was presented, made of food waste (according to a recipe by Aurore Bourguignon). Marion leads a new project called “El Barri Circular”, which explores the potential of food waste (recycling, composting, materials design) with the residents, shop and restaurant owners of Poblenou.


Ingredients for bag:
– 2g alginate
– 2g orange powder or coffee grounds
– 2g olive oil
– 33g water
– 5g glycerine
– spray with 7g CaCI2 in 100ml water
Mix all the ingredients and spread the mixture in a frame or mold. Let stand about 5 minutes. Use the calcium chloride solution spray, rinse with water and let dry a few days. Then use this material to make the bag by laser-cutting the parts according to the downloadable pattern.
Weaving stories
What we learned from our ITMA visit: the weaving loom developed by Frenchman Joseph Marie Jacquard in 1811 is the first mechanical system that can be programmed using perforated cards, ranking it in the history of technology as the ancestor of the computer or robot.


Weaving looms have since continued to evolve into imposing and entirely automated machines. These Jacquard looms 4.0 exhibited at ITMA produce most patterned fabric for clothes, furniture and house linens. Finally, as Marion reminds us, the engine of all this remains to “learn from human time vs the capacity of the machine”.
All creations and publications of Fabtextiles and Fabricademy can be downloaded from Open Source Circular Fashion
Fabtextiles also contributes to Materiom, a research platform and database of ingredients to cook with biomaterials