Chronique d’une makeuse en matériaux (28)
Publié le 24 avril 2018 par Caroline Grellier
Pour valoriser les sous-produits de la filière coton au Bénin, notre makeuse visite les usines, les cotonculteurs, se familiarise avec les machines, expérimente au labo… Et mise sur la cocréation.
Cotonou, correspondance (texte et images)
Au Bénin, chaleur, chaleur et dur labeur ! Bientôt deux mois que je suis arrivée au Pôle technologique de promotion des matériaux locaux (Potemat), laboratoire de recherche sur le campus de l’université d’Abomey-Calavi. J’y effectue un stage sous la direction de l’enseignant Chakirou Akanho Toukourou, pour valider un master design innovation société à l’université de Nîmes. Ma mission ici consiste à appuyer un projet de valorisation des sous-produits de la filière coton en matériaux locaux.
De Cotonou à Parakou, enquête de terrain
Dans les starting-blocks, plongée dans la filière coton ! Au menu de la phase 1 du projet : des tartines de textes et d’articles scientifiques à lire sous un ventilateur, pour tout comprendre de la filière, de ses enjeux, de son histoire, localiser les sous-produits peu, pas ou mal valorisés et identifier des opportunités de projet.
Ce gros boulot d’analyse, je l’ai reformulé graphiquement sous forme de posters de synthèse, compréhensibles par tous. Trois croquis d’usine et une mise en forme des différentes étapes permettent d’avoir une vision plus claire sur les sous-produits en question.

Et pour vérifier les données et mieux saisir les problématiques de la filière, rien de tel que des visites de terrain, à la rencontre de l’ensemble des acteurs, du champ de coton jusqu’aux usines de transformation. De quoi assouvir ma curiosité pour les machines…
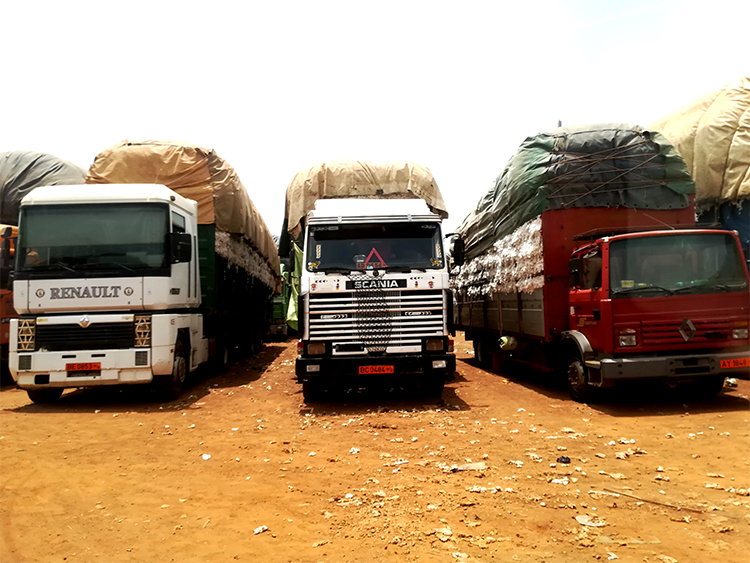
Après quelques entretiens à Cotonou, dans les bureaux des organismes en charge d’accompagner le développement de la filière et d’appuyer les cotonculteurs, direction Lokossa pour visiter la Compagnie béninoise de textile (CBT), la dernière usine textile du pays.
A post shared by Makery France (@makeryfr) on
En discutant avec le chef de production, j’ai complété mon schéma et découvert de nouvelles matières non valorisées dans la filière : les bouts de fil encollés par exemple, ou encore les cartons, c’est-à-dire les zones exposées des balles de coton qui deviennent dures au contact de l’humidité et de l’air extérieur.
J’ai assisté à toutes les étapes qui permettent la fabrication d’un fil de coton : battage, cardage, étirage, banc à broche et bobinage, puis ourdissage, encollage et tissage des écrus de coton. Du coton brut, jusqu’aux écrus acheminés en Côte d’Ivoire pour l’impression des fameux tissus wax, à la cote internationale.
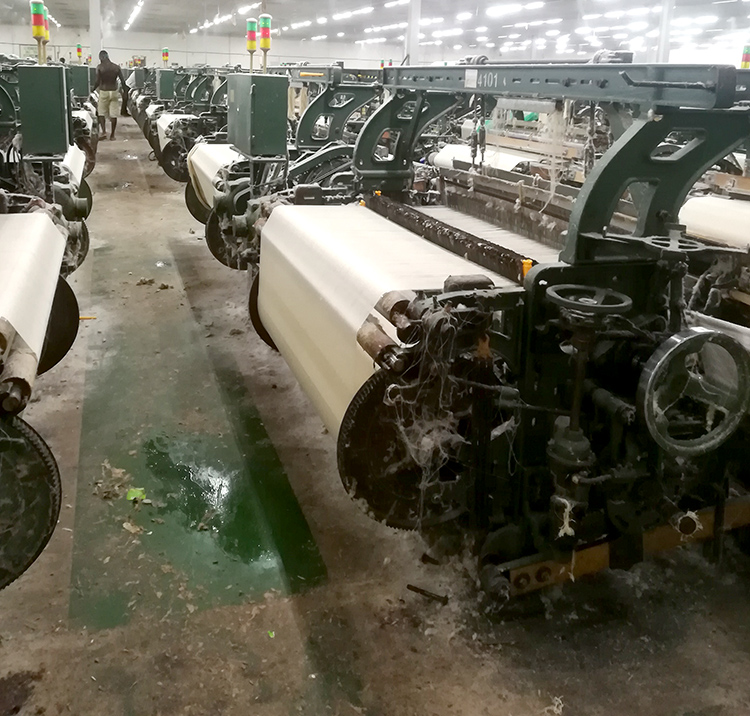
Seconde étape à Bohicon auprès d’une usine de trituration qui produit des tourteaux (des résidus de l’extraction de l’huile) et de l’huile de coton. Casque de chantier sur la tête, j’ai parcouru les différentes zones de transformation, depuis l’arrivée des graines de coton jusqu’à leur traitement.
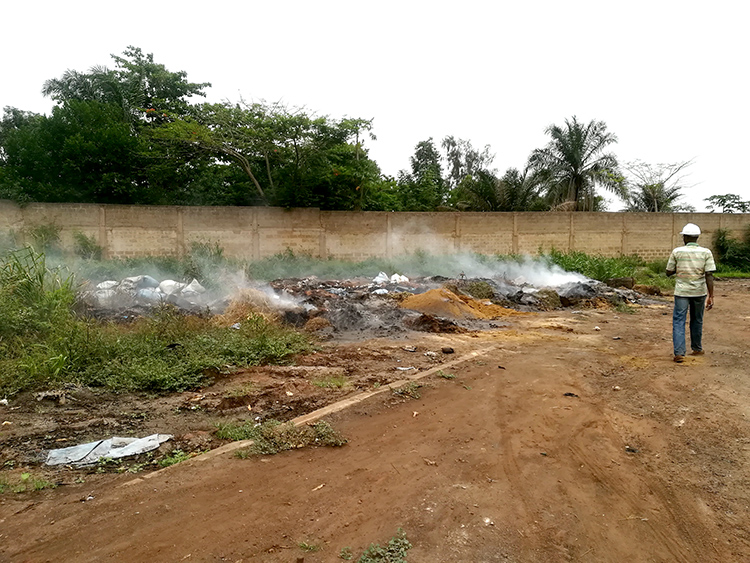
Là encore, des sous-produits sont jetés, considérés comme des déchets, alors que le potentiel est certain. Les déchets de fibre, les coques, les cendres de coque et les terres de filtration feront l’objet d’une exploration matériau. Et hop, dans le coffre de la voiture !
Troisième étape plus au nord du pays, à sept heures de route de Cotonou, dans les environs de Parakou, pour aller échanger avec les cotonculteurs dans leurs champs et recueillir leurs éventuels besoins en matériaux, leurs difficultés de gestion des tiges de cotonnier, leurs pratiques, comprendre leurs journées.
Avec mon accent français et mon débit de parole, pas toujours évident de se faire comprendre mais on finit toujours par y arriver. Valoriser les tiges de coton ? Le sujet qui divise ! Les agronomes militent pour un retour à la terre mais le broyage-enfouissage, indispensable pour éviter l’apparition de parasites, n’est pas à la portée des cotonculteurs, faute de matériel. De plus, d’autres études en Inde et aux Etats-Unis ont montré la pertinence économique de la valorisation des tiges de coton en panneaux de particules. Un projet a d’ailleurs été lancé en 2015 dans la sous-région ouest-africaine, mais est visiblement à l’arrêt. Enquête en cours…
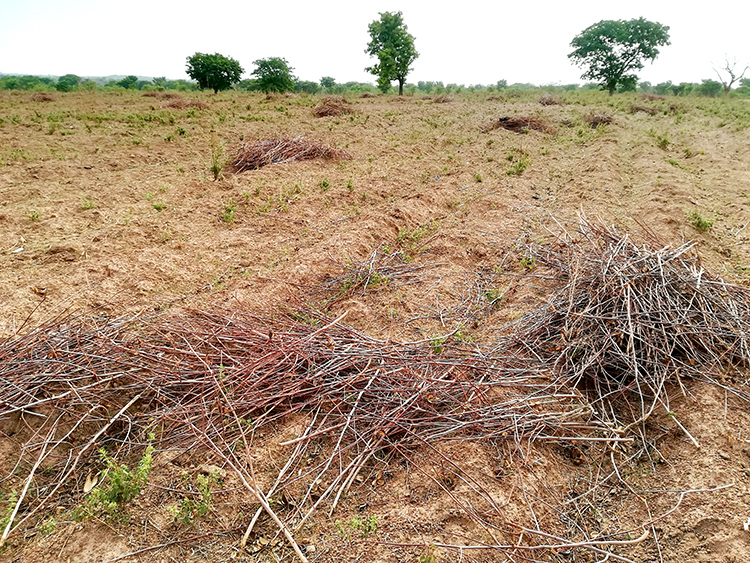
Enfin, étape clé de la filière : l’usine d’égrenage. Où il s’agit de séparer la graine des fibres de coton. Avec le brouhaha des machines, on se crie dans les oreilles pour tenter de poser des questions. Ici aussi, à chaque nettoyage des fibres de coton, des résidus sont déversés dehors.
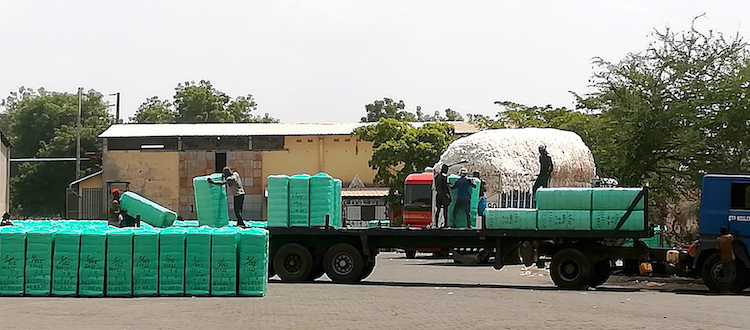
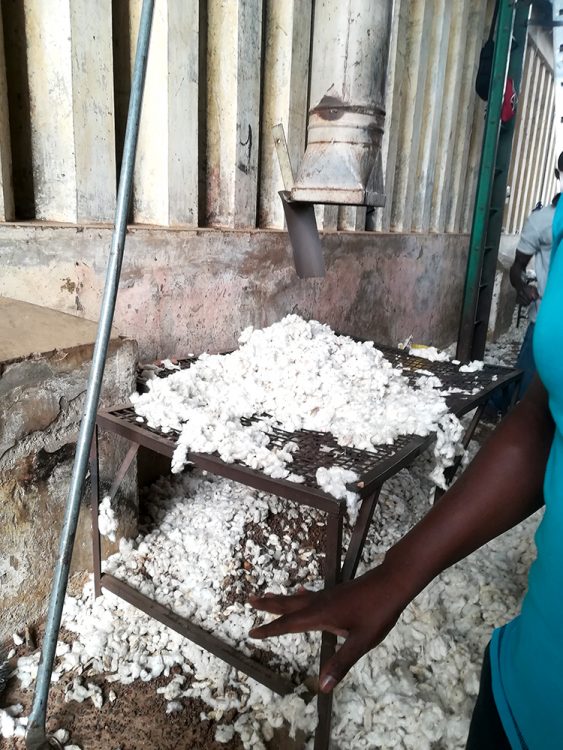
Je suis donc rentrée à Cotonou chargée de sacs d’échantillons et des idées plein la tête. Une étude efficace : avant d’aller sur le terrain, trois sous-produits avaient été identifiés. Après la mission, on en compte quatorze.
La suite ? Des ateliers de cocréation pour construire à plusieurs cerveaux les protocoles d’expérimentation des sous-produits en matériaux, en fonction des problèmes relevés sur le terrain.
Makers de machines
En parallèle, avec trois étudiants en génie mécanique de Cotonou, on réfléchit à transformer une presse à tuile en thermopresse, à adapter un broyeur pour les tiges de cotonnier, et à concevoir une défibreuse low-cost afin de nettoyer et étirer nos déchets de fibres.
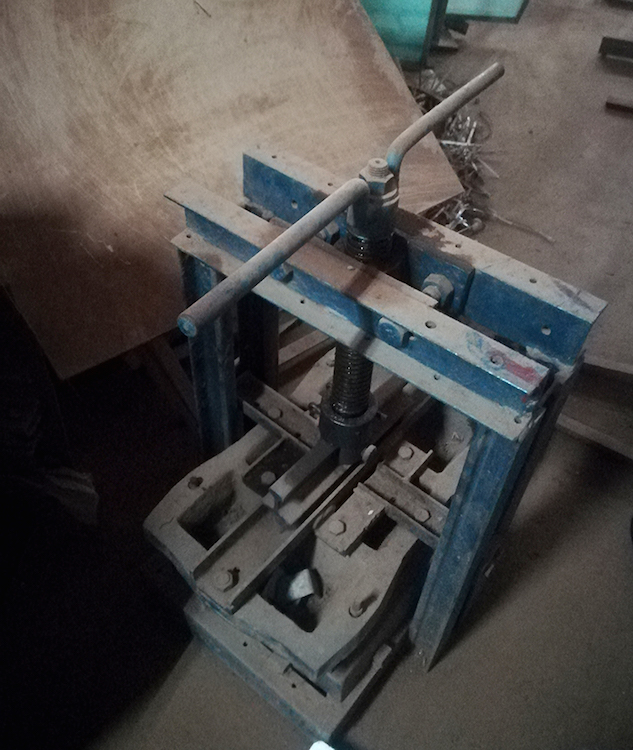
Après avoir fait l’inventaire des équipements et matériels de transformation agro-alimentaire présents dans l’atelier de l’école polytechnique d’Abomey-Calavi (Epac), nous avons réfléchi et finalisons les plans de conception cette semaine ! Tournevis et marteaux seront donc au rendez-vous de la prochaine chronique.
Retrouvez les précédentes chroniques d’une makeuse en matériaux